In route to a sustainable future
- Rodolfo
- Apr 11, 2020
- 3 min read

Fossil plants (coal and gas) and heavy industry (such as cement and steel production) are, currently, the largest contributor of CO2 emissions, with 27 and 8 Mt of total CO2 emissions, respectively, every year. In fact, the mining sector demands ca. 11% of global energy use. Although, several technologies have been developed to capture CO2 from flue gas streams and store CO2 in geologic environments, the deployment of such technologies have not been widely incentivised, mainly due to financial investment and the risk of an attractive profit return. This also means that we need to start analysing this problem from the perspective of CO2 emissions, and the capabilities of current process technologies to reduce it.
Transition to low-carbon technologies is essential to combat climate change. However, this will also lead to an increasing demand for strategic minerals and metals, which will require energy to be produced. This energy input will equate to a significant cost and an associated increase in CO2 emissions. For this reason, sustainable mining and mineral recycling are key to sustain a low-carbon future. In this context, metals such as rare earth elements, lithium, cobalt and others, are crucial for the development of the so-called low-carbon technologies such as windmill, solar panels and batteries. However, some of these metals have been considered as critical for the economy of Europe, which means that they have both a high supply risk (e.g. due to monopoly or geopolitical reasons) and have a high economic importance. While supply risk relates to sustainability recycling rates and monopolies on the production, high economic value relates to the overall demand.
The resources of these metals can be very large and, perhaps, also very well distributed. Theoretically speaking, they could be enough to cover future demands. However, the production of some of these metals is controlled by just some few countries. For instance, China is currently the largest rare earth producer, which leads to a supply problem… and the rare earths are key metals for developing all the technological devices you can imagine.
For this reason, metal recycling from solid waste residues can help to ensure a supply of critical metals especially for industrialised countries without primary production, like France, Belgium or Germany.
However, the separation of specific metals from their host solid matrix can be carried out by a chemical process at temperatures above 300 °C (the so-called Pyrometallurgical processes), and processes involving liquid solutions at temperatures between 20 – 200 °C (the so-called Hydrometallurgical processes), or a combination of both. Both two processing routes require a significant amount of energy, which is dominantly produced by the combustion of fossil fuels like oil, coal or natural gas. Furthermore, these processes are not exempted of producing large quantities of flue gases and solid/liquid waste residues, which also require energy to be further treated and/or disposed.
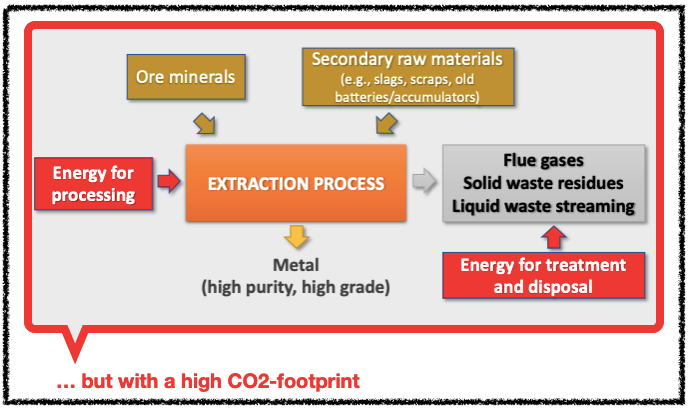
Current extractive process technologies are not so different than the one used by our ancestors, as you can see in the picture below. We must consider the fact that in the very near future we will start dealing with more complex and lower grade raw materials, and for this reason, innovation is indispensable to process minerals and metals in a more efficient and sustainable way.

Some interesting links:
Some scientific references:
[1] Billig et al. (2019). Non-fossil CO2 recycling—The technical potential for the present and future utilisation for fuels in Germany. J. CO2 Util. 30, 130–141. DOI: 10.1016/j.jcou.2019.01.012
Comments